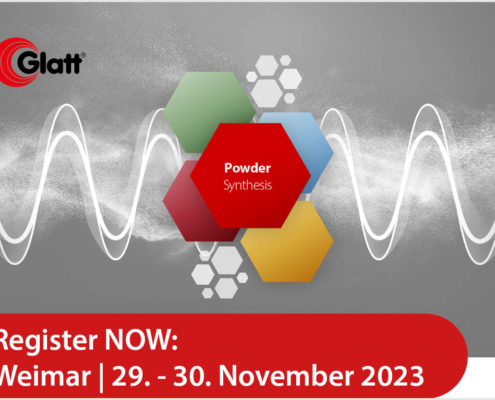
The innovative solution for your next generation of powder materials
Increasing global demands on the functionality and service life of products pose new challenges to materials and material development in all industries, including powder production. Our answer is Glatt powder synthesis.
From nano to micro: drying, coating and calcining in just one process step with synthesis reactors from Glatt. Produce and coat powder materials with new, previously unattained properties in the pulsating hot gas stream of the patented Glatt powder synthesis. Thanks to the particularly homogeneous thermal treatment at up to 1,300°C, ultra-fine powders produced in this way are free of hotspots, easily dispersible and free of undesirable hard aggregates. Benefit from very high heat and mass transfer rates in the reactor and from the ability to specifically determine the layer thickness, porosity and activity profiles of your powder particles. You have full flexibility to adjust the chemical composition of your powders, achieve extremely good homogeneity and a narrow particle size distribution. The continuous process is easily scalable to industrial applications. Secure our support to realize your product idea and access to innovative technology. Benefit from short development times for new materials using our facilities for collaboration. Laboratory trials and pilot tests in the Glatt Technology Center are your reliable express route to results for the fundamental feasibility of your product requirements and sample quantities for performance evaluation or marketing.
Take advantage of our technological expertise for your innovative particle design!
More long-term stability for battery materials through clever coating of anode/cathode material
Unique new optical effects and maximum protection for your paint and varnish pigments
Reduced material usage for your catalytically active powders through core-shell coating
Particles with precisely definable chemical composition in narrow particle size distributions
Microfine, extremely homogeneous powders through drying, core-shell coating and calcination in one step
Battery Powder
Materials
Active battery materials and solid electrolytes for solid state batteries
Ceramic Powder Materials
Innovative potentials for producing high-performance ceramics
Catalytic Powder Materials
Catalytic Innovative potentials for producing high-performance ceramics
Paint and Varnish Pigments
Effect and special pigments for completely new applications
The revolutionary technology of spray drying and spray calcination in a pulsating gas stream enables the precise design of completely new powder types with customized properties. Glatt powder synthesis is the innovative solution for increasing demands on the functionality and complexity of your materials. Discover our potential for the design of your primary particles. Get an overview of the range of applications for Glatt powder synthesis.
Benefit from all the services of the Glatt Group as a complete supplier of particle systems along the entire process chain.
NEW DOWNLOAD
Powder synthesis – Particle design optimizes battery materials
Glatt powder synthesis offers a versatile tool for the development and industrial production of innovative battery materials. The highly flexible technology opens up the possibility of producing and refining anode and cathode materials as well as solid electrolytes in just one step. The key to the effectiveness of this process is the special conditions in the pulsating hot gas flow.